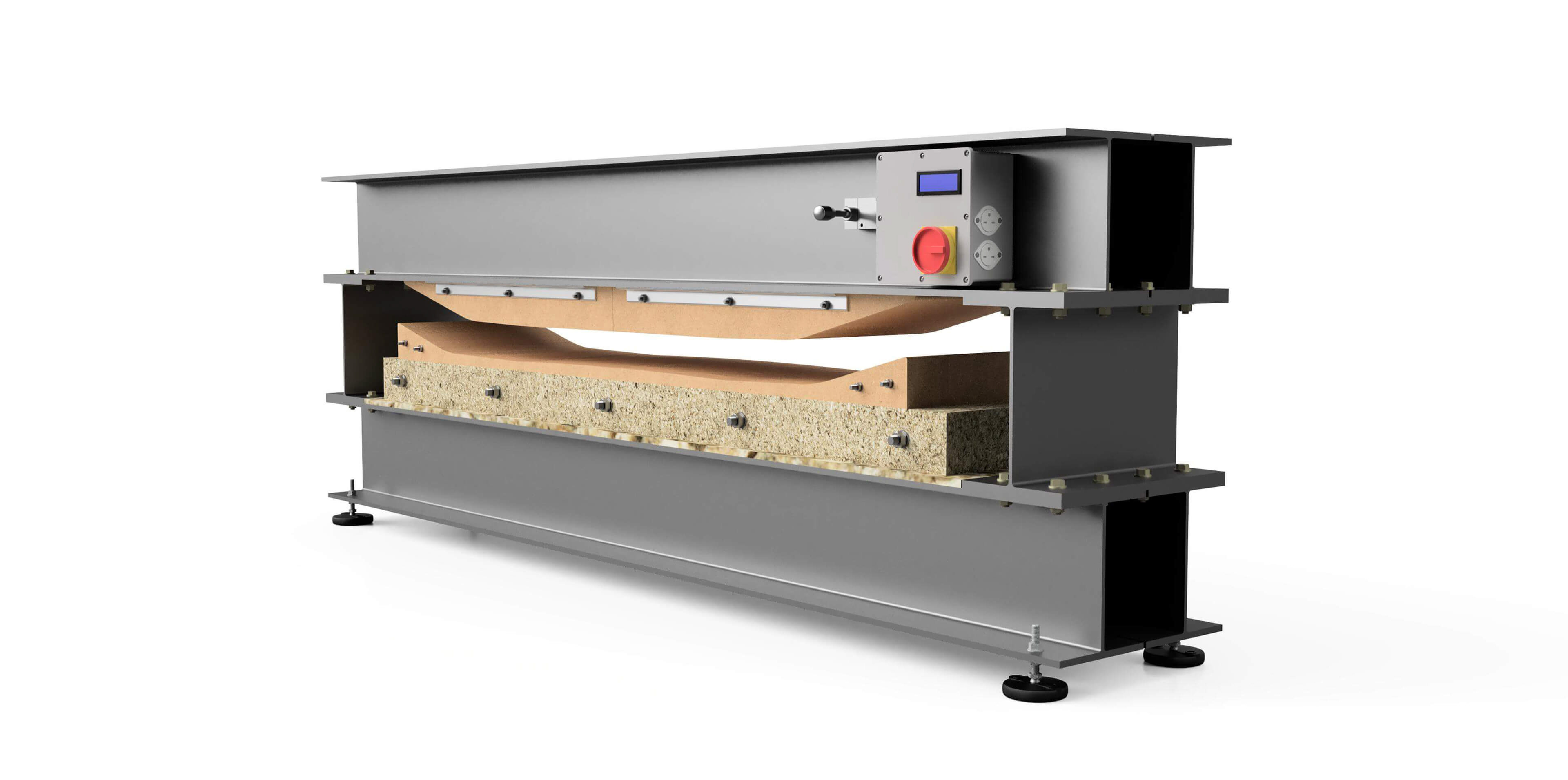
The largest piece of equipment, literally and figuratively, in manufacturing snowboards, is the press. The physical structure of a press is not that complicated. The press should be engineered to handle the stresses that the project requires and fit a budget. A bolt together design was chosen for it's simplicity and cost effectiveness. The press was designed to safely handle a stress of 30 tons, but in actual production is only operating at 6 tons. Total weight with molds and all required hardware is roughly 1500 lbs. A manual 4-way pneumatic valve controls air pressure and an Arduino based heat controller regulates the two silicone heat blankets operating at 240V. The Arduino based system allows the controls to be upgraded easily for more automation if and when needed.
Arduino Heat Blanket Controller for Snowboard Press
Snowboard Layup in Cassette
Snowboard press cavity
Snowboard Press
After finalizing the press frame design, development for the sub-assemblies began. The molds, bladder and cassette. Molds form the shape of the board and must be changed out when pressing a board of another size. MDF was selected as the mold material for it's strength and cost effectiveness. The molds were designed to use as little material as possible to aid in the change out and in production costs. A large vertically laminated block of particle board was squared on a CNC machine to create a flat base to support the bottom mold.
The parts for the press bladder took some time to source, but was worth the investment. Instead of a complex multi-bladder design, that is the norm for ski and snowboard pressing, a much simpler single-bladder design was developed. By carefully engineering the distance between the top and bottom molds the need for a complex "cat track" was eliminated. This method lowered the press working pressures and provided a much nicer composite. Also, mold change-over time was greatly reduced.
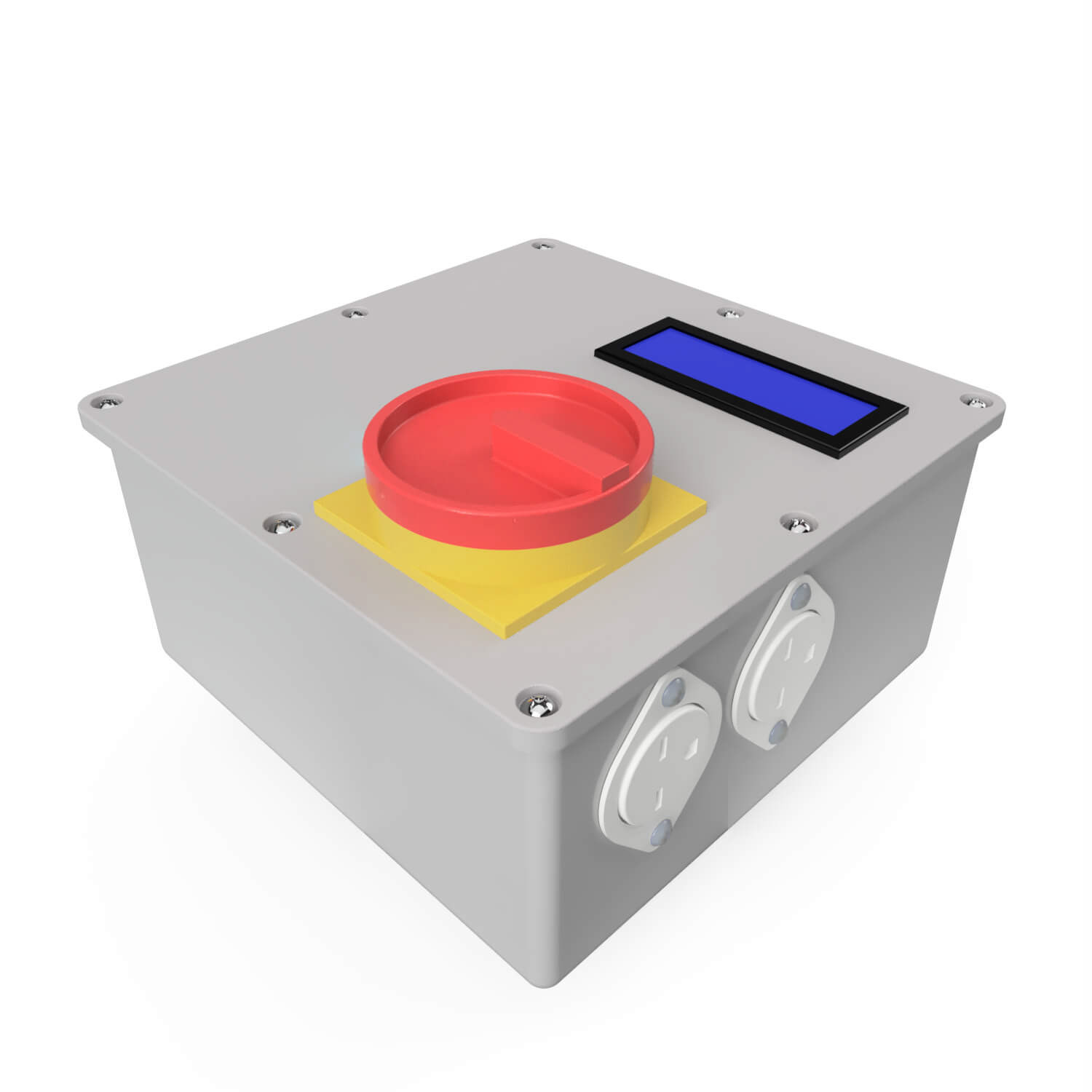
Snowboard Press Arduino Heat Blanket Control Box 3D Model Fusion 360
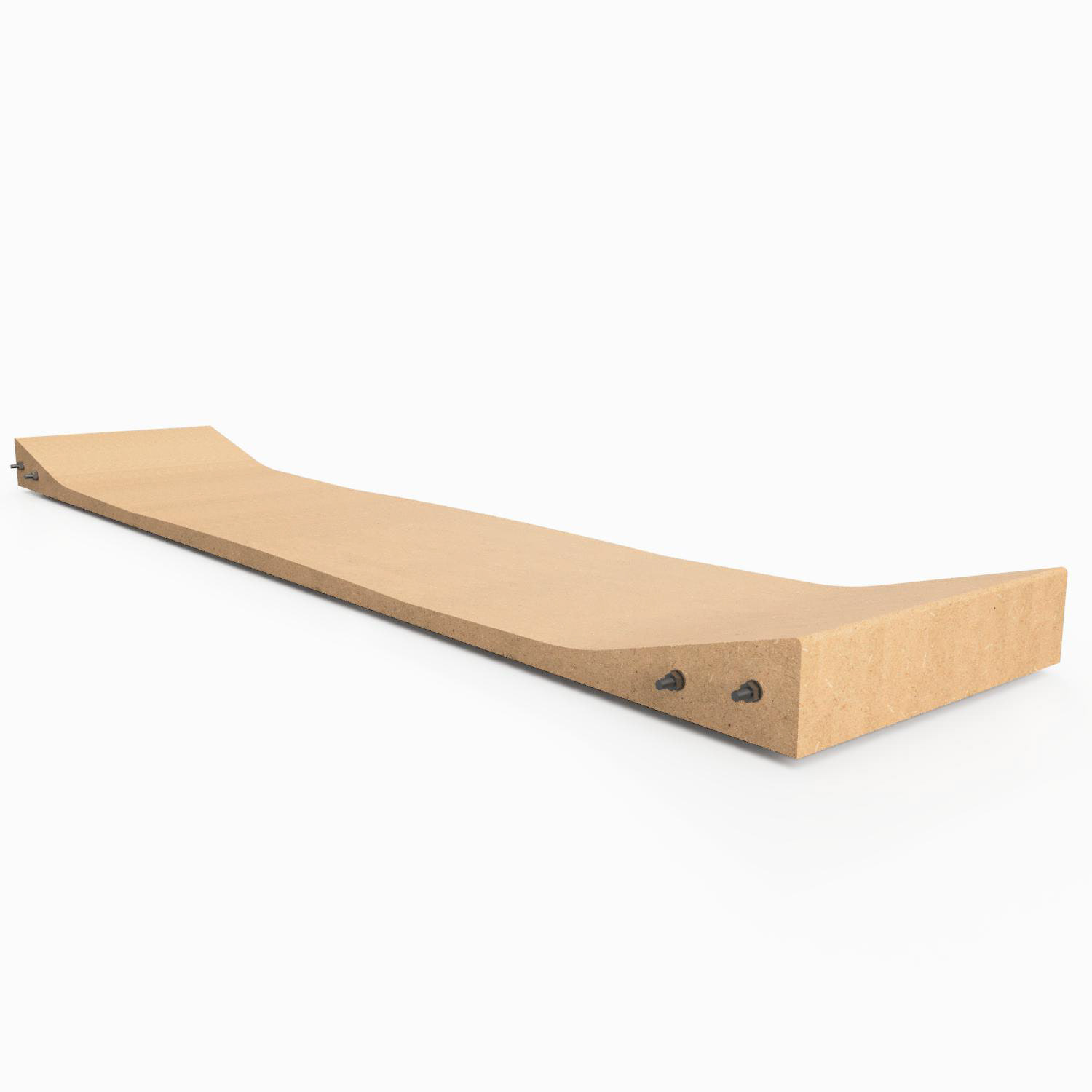
Snowboard Press Mold 3D Model Fusion 360
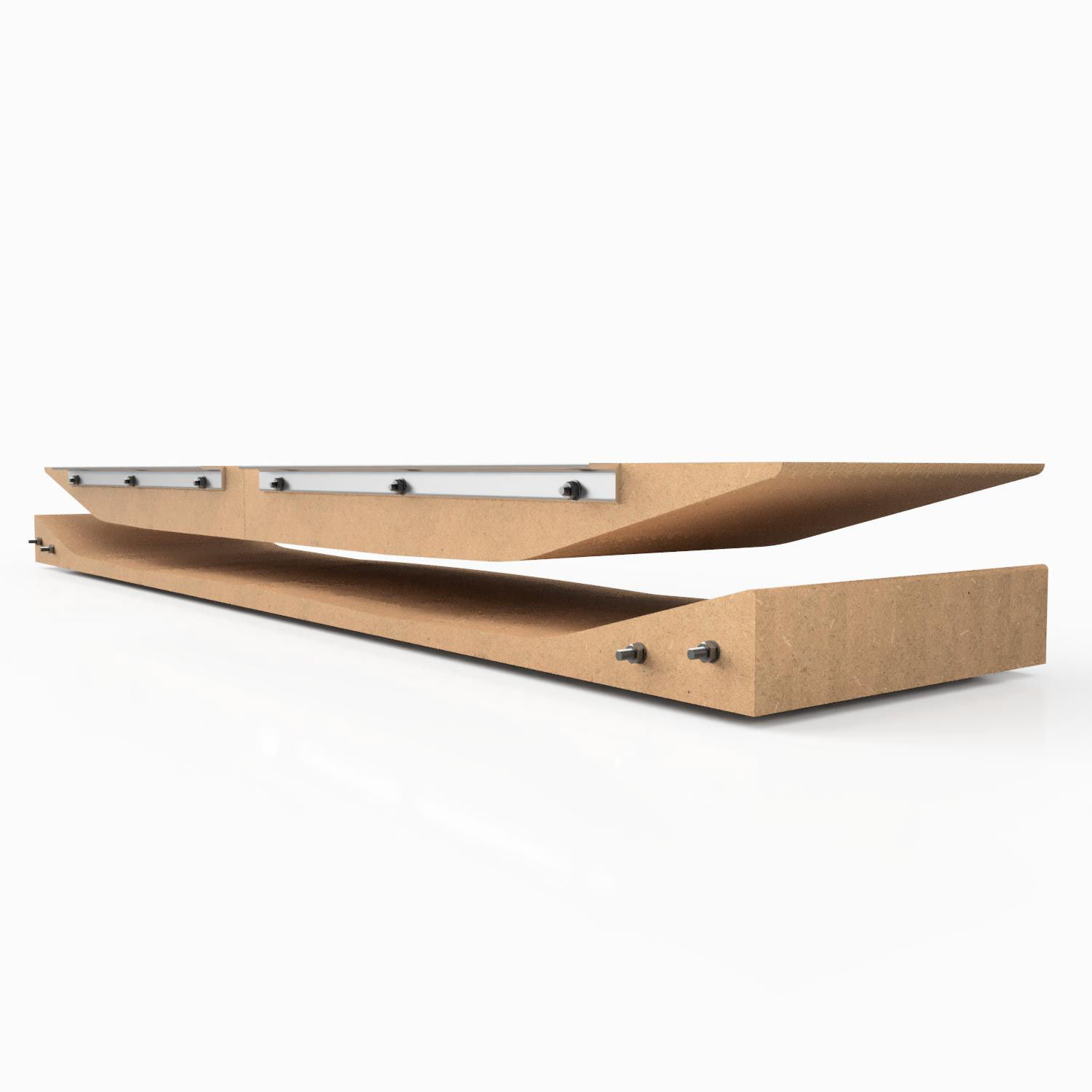
Snowboard Press Mold 3D Model Fusion 360
The final part of the pressing system was the cassette. The cassette is where the lamination is placed while in the press. All components in the lamination have to remain in their specific locations while the press develops pressure. A simple aluminum sheet was used with location pins to reference the board parts. This simplistic approach is very cost effective and allows multiple sized boards to be pressed in the same cassette. This also allows easy cleanup after a board has been pressed.
The over-all press design was a complete success. The finished product is cost effective, reliable, modular and completely upgradeable for future board designs. The simple mechanics of this pressing system produces extremely well made thermo compression composites.
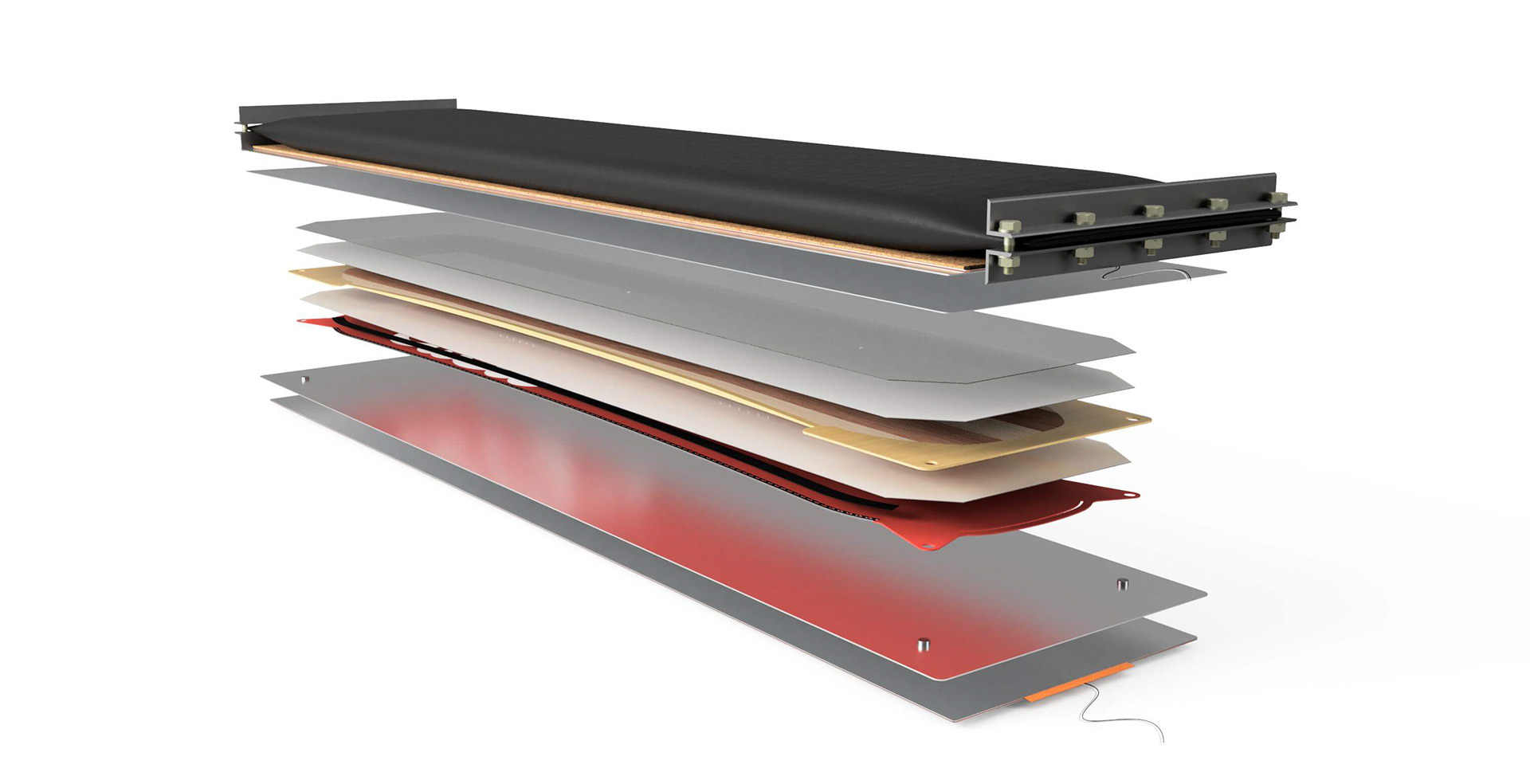
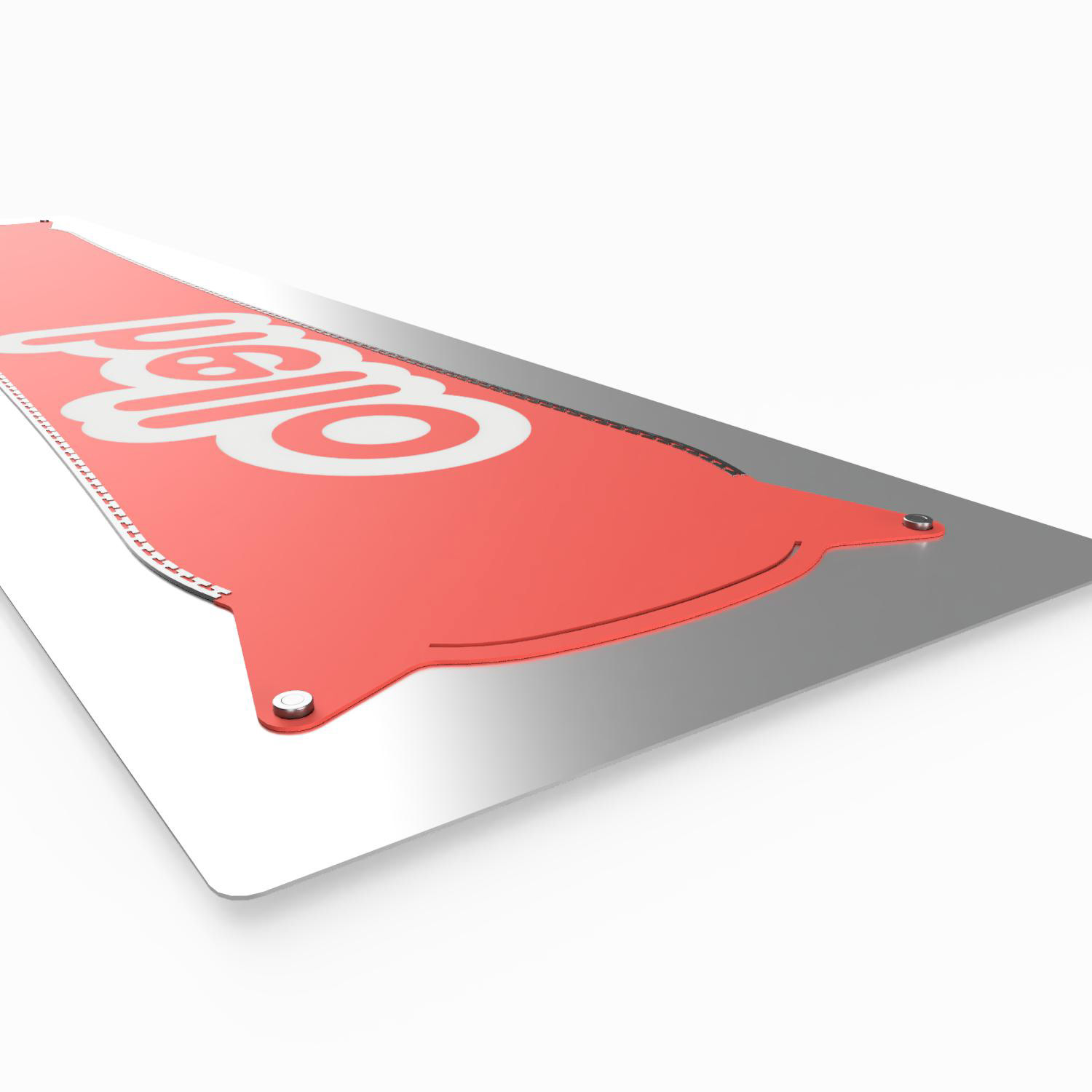
hello Snowboard Co. Snowboard Cassette with base 3D Model Fusion 360
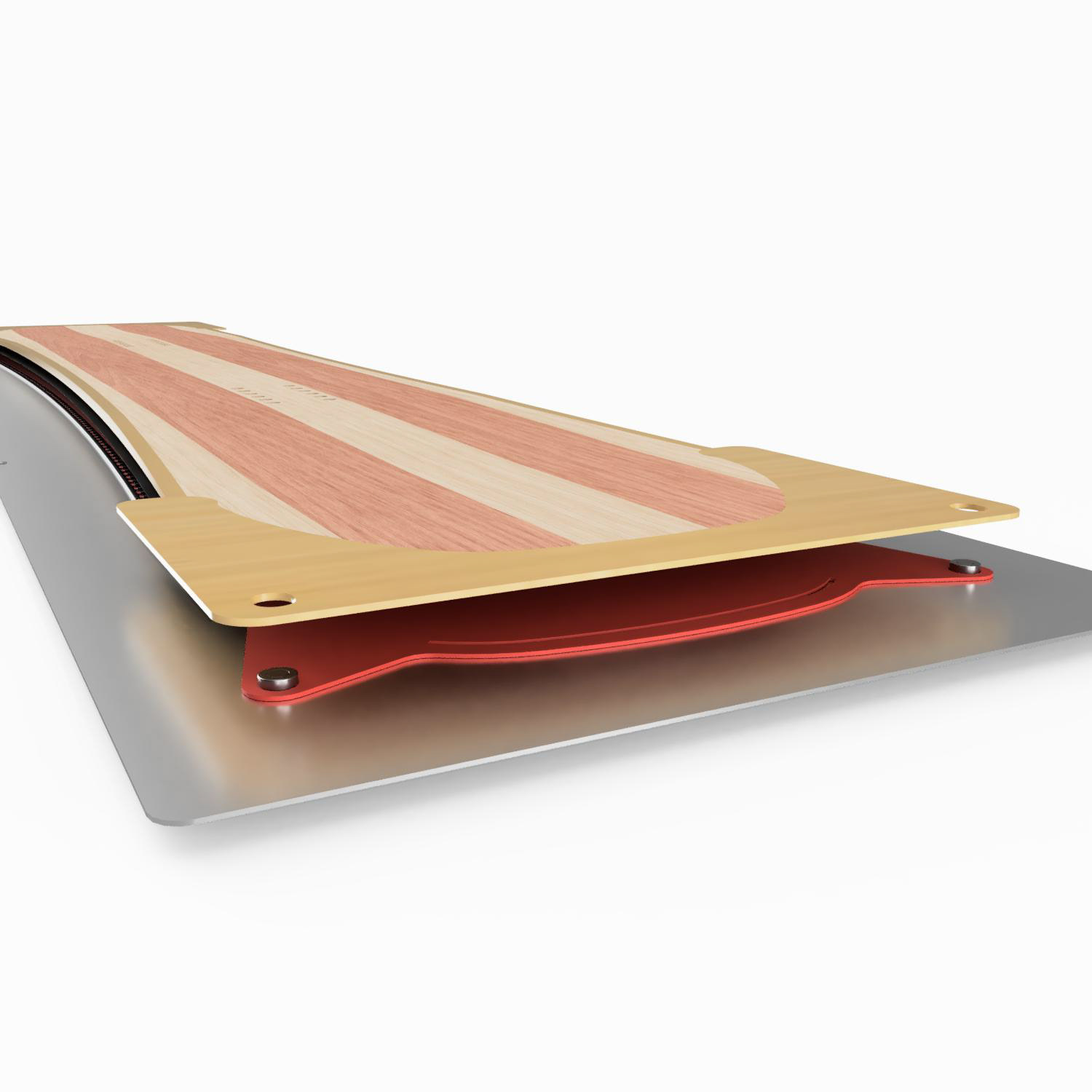